Brushless motors, also known as BLDC motors, are electric motors that use an electronic controller to switch the current in their stator windings. They consist of three main components: the rotor, stator, and electronic controller. The working principle of a brushless motor involves initial rotation, commutation, and maintaining rotation. Brushless motors offer several advantages over traditional brushed motors, including higher efficiency, longer lifespan, better performance, and lower maintenance.
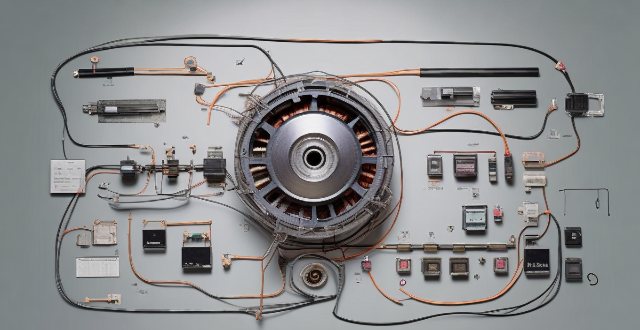
How Does a Brushless Motor Work?
A brushless motor, also known as a BLDC (Brushless Direct Current) motor, is an electric motor that uses an electronic controller to switch the current in its stator windings. This type of motor is becoming increasingly popular due to its high efficiency, reliability, and long lifespan compared to traditional brushed motors. Let's explore how a brushless motor works in detail:
Components of a Brushless Motor
A brushless motor consists of three main components:
1. Rotor: The rotor contains permanent magnets and is mounted on a shaft. It rotates inside the stator.
2. Stator: The stator is made up of coils of wire and is fixed in place. It surrounds the rotor.
3. Electronic Controller: The electronic controller regulates the flow of current through the stator windings, which creates a magnetic field that interacts with the rotor's permanent magnets.
Working Principle of a Brushless Motor
The working principle of a brushless motor can be broken down into the following steps:
Step 1: Initial Rotation
When power is applied to the stator windings, it creates a magnetic field that interacts with the permanent magnets on the rotor. This interaction causes the rotor to start rotating.
Step 2: Commutation
As the rotor rotates, sensors or hall effect devices detect its position relative to the stator windings. This information is sent to the electronic controller, which then adjusts the current flowing through the stator windings accordingly. This process is called commutation, and it ensures that the correct winding is energized at the right time to maintain rotation.
Step 3: Maintaining Rotation
The electronic controller continues to monitor the rotor's position and adjust the current flowing through the stator windings accordingly. This process repeats continuously, maintaining the rotation of the rotor and generating torque.
Advantages of Brushless Motors
Brushless motors offer several advantages over traditional brushed motors, including:
- Higher Efficiency: Brushless motors have higher efficiency ratings than brushed motors because they have fewer losses due to friction and heat generation.
- Longer Lifespan: Since there are no brushes rubbing against the commutator, brushless motors have a longer lifespan than brushed motors.
- Better Performance: Brushless motors provide better performance in terms of speed, torque, and response time compared to brushed motors.
- Lower Maintenance: Brushless motors require less maintenance than brushed motors because they have fewer moving parts that can wear out over time.
In conclusion, a brushless motor works by using an electronic controller to regulate the flow of current through its stator windings, creating a magnetic field that interacts with the rotor's permanent magnets. This interaction causes the rotor to rotate, generating torque and powering various applications such as drones, electric vehicles, and industrial machinery.