The lifespan of a DC brushed motor is influenced by mechanical wear, electrical stress, thermal effects, and environmental factors. To extend its operational life, strategies like regular maintenance, proper sizing, protection circuitry, adequate cooling, and maintaining cleanliness are recommended.
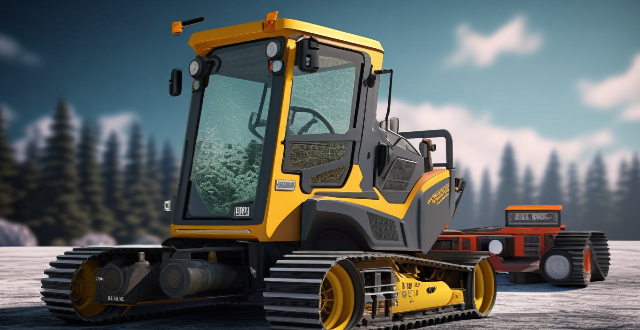
Factors Affecting the Lifespan of a DC Brushed Motor
The lifespan of a DC brushed motor is influenced by several factors, which can be mitigated to extend the motor's operational life. These factors include:
1. Mechanical Wear and Tear
- Brushes: The brushes in a DC brushed motor wear out over time due to friction with the commutator. This can lead to increased resistance and reduced efficiency.
- Bearings: Bearings are another mechanical component that experiences wear over time, leading to increased friction and reduced motor performance.
2. Electrical Stress
- Overloading: Operating the motor beyond its rated capacity can cause excessive heat and stress on the windings, leading to premature failure.
- Voltage Spikes: Exposure to high voltage spikes can damage the windings and insulation, reducing the motor's lifespan.
3. Thermal Effects
- Overheating: Prolonged operation at high temperatures can degrade the insulation on the windings, leading to short circuits and motor failure.
- Cooling: Inadequate cooling can exacerbate thermal effects, further reducing the motor's lifespan.
4. Environmental Factors
- Dust and Dirt: Accumulation of dust and dirt can interfere with the mechanical components, increasing wear and tear.
- Corrosion: Exposure to humidity or corrosive substances can damage the motor's components, reducing its lifespan.
Mitigation Strategies
To mitigate these factors and extend the lifespan of a DC brushed motor, consider the following strategies:
Mechanical Wear and Tear
- Regular Maintenance: Periodically inspect and replace worn-out brushes and bearings to maintain optimal performance.
- Lubrication: Use appropriate lubricants to reduce friction and wear on bearings and other moving parts.
Electrical Stress
- Proper Sizing: Ensure that the motor is properly sized for the application to avoid overloading and excessive electrical stress.
- Protection Circuitry: Incorporate surge protection and voltage regulation circuitry to protect against voltage spikes and fluctuations.
Thermal Effects
- Adequate Cooling: Ensure proper cooling mechanisms are in place, such as fans or heat sinks, to prevent overheating.
- Thermal Management: Implement thermal management strategies, like duty cycling or reducing load, to control operating temperatures.
Environmental Factors
- Cleanliness: Maintain a clean environment around the motor to prevent dust and dirt accumulation.
- Protective Coatings: Apply protective coatings or seals to vulnerable components to prevent corrosion and damage from environmental factors.
By addressing these factors and implementing appropriate mitigation strategies, you can significantly extend the lifespan of a DC brushed motor and ensure reliable operation over time.