When selecting a drive motor for your application, considerWhen selecting a drive motor for your application, considerrque and speed, power duty cycle, cost, size, control compatibility, safety compliance, maintenance, and manufacturer reputation. This comprehensive guide helps ensure you choose a motor that meets your needs effectively and efficiently.
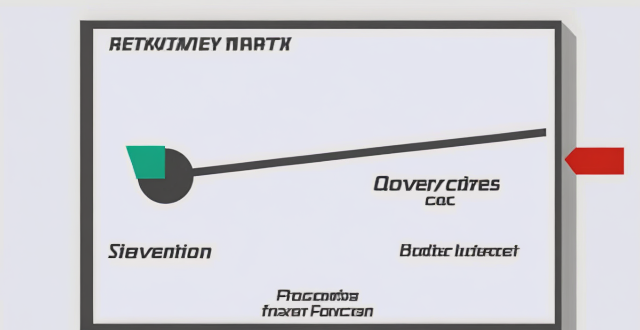
Choosing the Right Drive Motor for Your Application
When selecting a drive motor for your application, it's crucial to consider several factors to ensure optimal performance and efficiency. Here's a comprehensive guide to help you make an informed decision:
1. Determine the Required Torque and Speed
- Torque Requirements: Calculate the torque needed to overcome static friction and any additional load. This will dictate the minimum torque rating of the motor.
- Speed Requirements: Assess the desired operating speed range, including startup and maximum speed.
2. Consider the Power Source
- Electric Motors: Suitable for applications with access to electricity.
- Hydraulic Motors: Useful in applications where a pressurized fluid is already in use.
- Pneumatic Motors: Ideal for places with compressed air supply.
3. Evaluate the Environment
- Temperature: Ensure the motor can operate within the temperature range of your environment.
- Dust and Contaminants: Choose a motor with appropriate sealing and protection against particles.
- Vibration: Select a motor designed to withstand vibration if your application is prone to it.
4. Understand Duty Cycle and Start/Stop Frequency
- Continuous or Intermittent Use: Some motors are designed for continuous operation, while others are better suited for intermittent use.
- Start/Stop Frequency: If frequent starts and stops are expected, choose a motor that can handle such cycles without overheating.
5. Budget and Cost Considerations
- Initial Cost: The upfront cost of the motor itself.
- Operating Costs: Include energy consumption and maintenance expenses.
- Lifespan: A more expensive motor may have a longer lifespan, reducing replacement costs over time.
6. Physical Size and Weight
- Space Constraints: Ensure the motor fits within the allocated space in your machinery.
- Weight Capacity: The motor should be able to support the weight of the connected load.
7. Control and Compatibility
- Control Systems: Check compatibility with existing control systems like variable frequency drives (VFDs) or programmable logic controllers (PLCs).
- Interface Options: Look for motors with communication interfaces that match your system's requirements.
8. Safety and Regulatory Compliance
- Safety Standards: Ensure the motor meets relevant safety standards for your industry and region.
- Regulatory Compliance: Check for any legal requirements or certifications needed for your application.
9. Maintenance and Serviceability
- Maintenance Requirements: Some motors require regular maintenance, which can impact operational downtime and costs.
- Service Network: Consider availability of service centers and expertise for the specific motor type in your area.
10. Manufacturer Reputation and Support
- Reputation: Choose a reputable manufacturer known for quality products and customer satisfaction.
- Technical Support: Look for manufacturers offering strong technical support and resources to assist with installation and troubleshooting.
By considering these factors, you can select a drive motor that will meet the needs of your application effectively and efficiently. Always refer to the manufacturer's specifications and consult with professionals if necessary to make the best choice for your specific situation.