Permanent magnet motors (PMMs) and induction motors (IMs) are two common types of electric motors used in various applications. The cost difference between them is often a significant factor in deciding which one to use. PMMs are known for their high efficiency, compact size, and low noise levels, while IMs are simpler and more robust. The cost difference depends on factors such as size, power rating, materials used, and manufacturing processes. Generally, PMMs are more expensive than IMs of equivalent size due to material costs, manufacturing processes, efficiency and performance requirements, and market demand and availability. When choosing between these two types of motors, it is essential to consider both the technical requirements and budget constraints of your specific application.
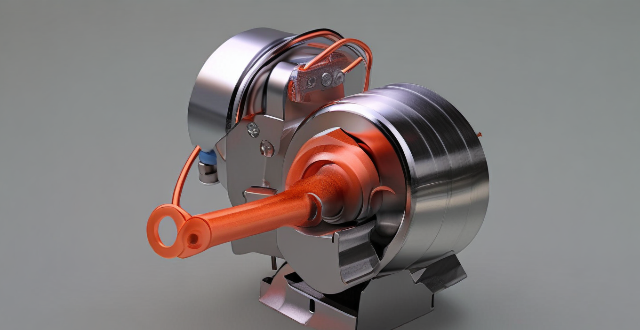
Cost Comparison between Permanent Magnet Motors and Induction Motors
Introduction
Permanent magnet motors (PMMs) and induction motors (IMs) are two common types of electric motors used in various applications. Both have their advantages and disadvantages, but the cost difference between them is often a significant factor in deciding which one to use. In this article, we will explore the typical cost difference between a permanent magnet motor and an equivalent size induction motor.
Permanent Magnet Motors
Permanent magnet motors are known for their high efficiency, compact size, and low noise levels. They use powerful magnets to generate a magnetic field that interacts with the current-carrying conductors to produce torque. PMMs are often used in applications where high efficiency and precise control are required, such as in electric vehicles, wind turbines, and machine tools.
Induction Motors
Induction motors, on the other hand, are simpler and more robust than PMMs. They rely on electromagnetic induction to generate torque, using a rotating magnetic field produced by alternating current flowing through the stator windings. IMs are commonly used in industrial applications, such as pumps, fans, and conveyor belts, where reliability and durability are crucial.
Cost Difference
The cost difference between PMMs and IMs depends on several factors, including the size, power rating, materials used, and manufacturing processes. Generally speaking, PMMs are more expensive than IMs of equivalent size due to the following reasons:
1. Material Costs: PMMs require rare earth magnets, which are more expensive than the copper or aluminum windings used in IMs. The cost of these magnets can significantly impact the overall cost of the motor.
2. Manufacturing Processes: PMMs typically involve more complex manufacturing processes than IMs, which can increase the production costs. This includes the assembly of the magnets and the precise placement of the rotor and stator components.
3. Efficiency and Performance: PMMs offer higher efficiency and better performance than IMs, which can justify their higher cost in certain applications. However, for some applications where efficiency is not a critical factor, IMs may be a more cost-effective option.
4. Market Demand and Availability: The demand for rare earth magnets used in PMMs can fluctuate based on market trends and supply chain disruptions. This can affect the availability and cost of these materials, ultimately impacting the cost of PMMs.
Conclusion
In conclusion, while PMMs offer several advantages over IMs in terms of efficiency and performance, they generally come at a higher cost. The exact cost difference between a permanent magnet motor and an equivalent size induction motor depends on various factors, including material costs, manufacturing processes, efficiency requirements, and market demand. When choosing between these two types of motors, it is essential to consider both the technical requirements and budget constraints of your specific application.