Choosing the right AC stepping motor requires understanding project needs, selecting the appropriate motor type, ensuring compatibility with control systems, considering physical constraints, evaluating performance characteristics, accounting for environmental factors, managing budgetary considerations, relying on supplier support and reputation, and conducting thorough testing.
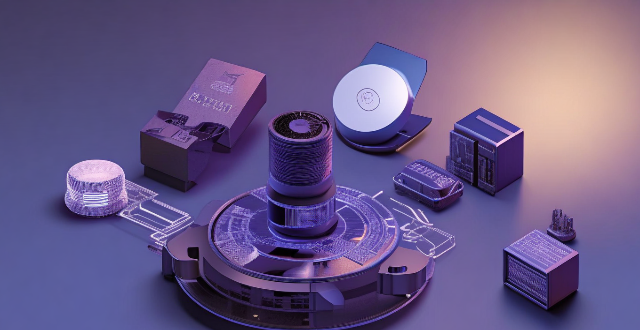
How to Choose the Right AC Stepping Motor for Your Project
Choosing the right AC stepping motor for your project involves considering several factors that will ensure the motor meets the requirements of your application. Here's a detailed guide to help you make an informed decision:
1. Understanding Your Project Needs
- Torque Requirements: Determine the amount of torque needed to move your load. This is crucial as it affects the size and type of motor you'll need.
- Speed Specifications: Consider the speed at which your motor needs to operate. Different applications require different speeds, from slow and precise movements to high-speed operations.
- Resolution: The resolution, or step angle, determines the motor’s precision. A smaller step angle allows for finer control but may also limit the maximum speed.
2. Selecting the Motor Type
- Bipolar vs. Unipolar Motors: Bipolar motors can be driven in both forward and reverse directions using a single coil, while unipolar motors require two coils. Decide based on control complexity and directional needs.
- Integrated vs. Non-integrated Drivers: Integrated drivers offer a compact solution with less external hardware, but non-integrated drivers provide more flexibility and power options.
3. Compatibility with Control System
- Driver Compatibility: Ensure that the motor is compatible with your chosen driver. This includes matching voltage levels and signal types (e.g., TTL, CMOS).
- Interface Options: Consider how you will interface the motor with your control system. This could involve serial communications, parallel ports, or dedicated stepper motor controllers.
4. Physical Constraints
- Size Restrictions: The physical dimensions of the motor must fit within the space available in your project enclosure.
- Weight Considerations: The weight of the motor should be suitable for the load it needs to move, without causing excessive strain or wear.
5. Performance Characteristics
- Holding Torque: The holding torque is the amount of torque a motor can apply when it is not moving. It needs to be sufficient to hold the load against gravity or any other forces acting upon it.
- Dynamic Torque: This is the torque a motor can apply while it is moving. It must be enough to accelerate and decelerate the load within the required time frame.
6. Environmental Factors
- Temperature Range: Make sure the motor can operate effectively within the temperature range of your project environment.
- Dust and Moisture: If your project is in a dusty or moist environment, consider a motor with appropriate sealing and protection against corrosion.
7. Budgetary Considerations
- Cost of the Motor: Evaluate the cost of the motor itself, including any additional features that might drive up the price.
- Operating Costs: Consider the long-term costs such as energy consumption, maintenance, and potential replacements.
8. Supplier Support and Reputation
- Manufacturer Support: Look for manufacturers who offer good technical support and have a reputation for quality products.
- Warranty and Returns: Check the warranty period and return policy in case the motor does not meet your expectations or fails prematurely.
9. Testing and Validation
- Prototyping: Before finalizing your choice, test the motor in a prototype setup if possible to validate its performance in real conditions.
- Feedback from Peers: Seek advice from peers or experts who have experience with similar projects to gain insights into potential issues or recommendations.
By carefully considering these factors, you can select an AC stepping motor that will reliably serve the needs of your project while fitting within your budget and technical constraints.