The article provides a comprehensive overview of how an electromagnetic motor works, including its basic components such as the stator, rotor, bearings, commutator (in DC motors), and armature (in AC motors). It explains the operating principles in four steps: applying electrical energy to create a magnetic field around the stator coils, the interaction between the magnetic fields of the stator and rotor causing the Lorentz force, the rotation of the rotor as it tries to align its magnetic poles with those of the stator, and maintaining consistent rotation through current reversal by the commutator in DC motors or changing polarity in AC motors. The article also discusses different types of electromagnetic motors like DC motors, AC motors, stepper motors, synchronous motors, and induction motors, highlighting their unique characteristics and suitability for various applications based on efficiency, power requirements, and control complexity.
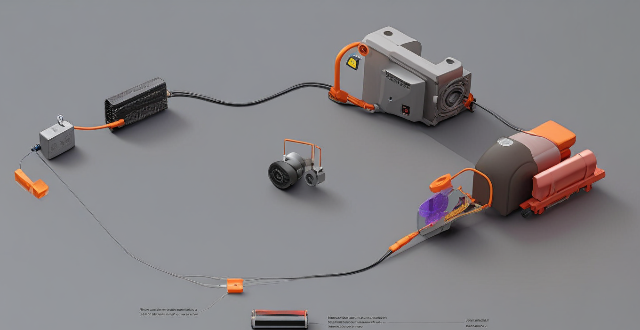
How Does an Electromagnetic Motor Work?
An electromagnetic motor is a type of electric motor that uses the principles of electromagnetism to convert electrical energy into mechanical energy. Here's how it works:
Basic Components
- Stator: The stationary part of the motor, which contains coils of wire that produce a magnetic field when an electric current flows through them.
- Rotor: The rotating part of the motor, which is made up of a series of permanent magnets or electromagnets.
- Bearings: Support the rotor and allow it to rotate smoothly within the stator.
- Commutator (in DC motors): A device that reverses the current in the rotor windings as they rotate, maintaining a consistent direction of rotation.
- Armature (in AC motors): The rotating part of the motor, which carries the windings through which current flows.
Operating Principles
Step 1: Applying Electrical Energy
When an electric current is applied to the stator coils, it creates a magnetic field around each coil.
Step 2: Interaction Between Magnetic Fields
The magnetic fields produced by the stator interact with the magnetic fields of the rotor. This interaction causes the rotor to experience a force known as the Lorentz force, which tends to align the rotor's magnetic poles with those of the stator.
Step 3: Rotation of the Rotor
As the rotor tries to align its magnetic poles with those of the stator, it begins to rotate. The speed and direction of this rotation depend on various factors, including the frequency and amplitude of the alternating current supplied to the stator windings, as well as the design of the motor itself.
Step 4: Maintaining Consistent Rotation
In DC motors, the commutator reverses the current in the rotor windings as they pass each stator coil, ensuring that the rotor continues to turn in the same direction. In AC motors, the changing polarity of the stator windings due to the alternating current maintains consistent rotation.
Types of Electromagnetic Motors
There are several types of electromagnetic motors, including:
- DC Motors: Use direct current and typically have a commutator to reverse the current in the rotor windings.
- AC Motors: Use alternating current and can be either single-phase or three-phase.
- Stepper Motors: Move in precise steps rather than continuously, making them ideal for applications requiring accurate positioning.
- Synchronous Motors: Operate at a constant speed determined by the frequency of the alternating current supply.
- Induction Motors: Use electromagnetic induction to create a rotating magnetic field in the rotor without physical contact between the rotor and stator.
Each type of electromagnetic motor has its own unique characteristics and is suited for different applications based on factors such as efficiency, power requirements, and control complexity.