Controllers play a critical role in electric drive motors, regulating speed, torque, and direction while providing protection against faults. PID, vector control, and FOC controllers are common types used across industries like robotics, automation, transportation, and manufacturing.
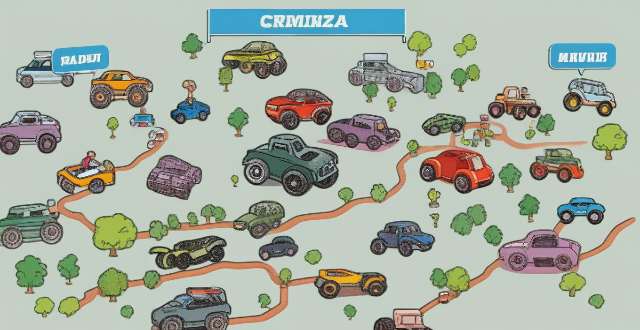
The Role of Controllers in Electric Drive Motors
Electric drive motors are an essential component of many modern machines and systems, providing the necessary power to perform various tasks. However, these motors cannot function effectively without a controller, which plays a crucial role in their operation. In this article, we will discuss the role of controllers in electric drive motors.
What is a Controller?
A controller is an electronic device that regulates the speed, torque, and direction of an electric drive motor. It receives input signals from sensors or other sources and processes them to generate output signals that control the motor's operation. The controller can be implemented using analog or digital circuits, depending on the application requirements.
The Importance of Controllers
Controllers are essential for several reasons:
* Speed Control: Controllers allow users to adjust the speed of electric drive motors according to their needs. This is particularly useful in applications where precise speed control is required, such as in robotics or automation systems.
* Torque Control: Controllers also enable users to control the amount of torque generated by the motor. This is important for applications where varying loads need to be handled, such as in cranes or elevators.
* Direction Control: Controllers can reverse the direction of rotation of electric drive motors, allowing machines to move backward or forward as needed.
* Protection: Controllers provide protection against overcurrent, overvoltage, and other faults that could damage the motor or cause safety issues. They monitor the motor's performance and shut it down if any abnormal conditions are detected.
Types of Controllers
There are several types of controllers used in electric drive motors, including:
* Proportional-Integral-Derivative (PID) Controllers: These controllers use mathematical algorithms to calculate the error between the desired and actual motor output and adjust the motor's response accordingly. PID controllers are widely used in industrial applications due to their accuracy and flexibility.
* Vector Control Controllers: These controllers use advanced techniques to control the motor's speed and torque independently, allowing for more precise control than traditional PID controllers. Vector control controllers are commonly used in high-performance applications such as electric vehicles and wind turbines.
* Field-Oriented Control (FOC) Controllers: FOC controllers use complex algorithms to control the motor's magnetic field orientation, resulting in improved efficiency and performance. FOC controllers are often used in servo drives and other high-precision applications.
Applications of Electric Drive Motors with Controllers
Electric drive motors with controllers have numerous applications across various industries, including:
* Robotics: Robots require precise control over their movements, making controllers essential for their operation.
* Automation Systems: Automation systems rely on electric drive motors to perform repetitive tasks accurately and efficiently. Controllers play a crucial role in ensuring that these systems operate smoothly.
* Transportation: Electric vehicles use electric drive motors with controllers to provide power and control over their movement. Similarly, elevators and escalators use controllers to ensure safe and reliable operation.
* Manufacturing: Manufacturing processes often require precise control over machinery, making controllers essential for producing high-quality products consistently.
In conclusion, controllers play a critical role in the operation of electric drive motors by providing precise control over their speed, torque, and direction. They also offer protection against faults and failures that could damage the motor or pose safety risks. With advancements in technology, controllers continue to evolve, enabling electric drive motors to perform increasingly complex tasks with greater efficiency and reliability.