Internal rotor motors operate through the interaction of magnetic fields produced by their stator and rotor components, generating rotational force and torque. They offer advantages such as high efficiency and precise speed control but also have drawbacks like increased complexity and maintenance requirements.
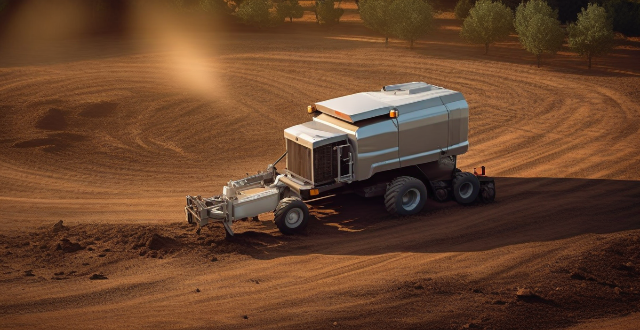
Introduction to Internal Rotor Motors
An internal rotor motor is a type of electric motor where the rotor (the moving part) is located inside the stator (the stationary part). The rotor typically consists of a series of windings or permanent magnets that interact with the magnetic field produced by the stator to generate motion. In this answer, we will explore how an internal rotor motor works in detail.
Basic Components of an Internal Rotor Motor
Stator
The stator is the outer shell of the motor and remains stationary during operation. It consists of a series of coils or magnets that produce a magnetic field when energized.
Rotor
The rotor is the inner core of the motor and rotates within the stator. It can be made up of windings or permanent magnets, depending on the design.
Bearings
Bearings support the rotor and allow it to rotate smoothly within the stator. They are essential for minimizing friction and wear during operation.
Commutator/Slip Rings (for wound rotor motors)
In wound rotor motors, commutators or slip rings are used to transfer electrical current to the rotor windings without physical contact between the rotor and stator.
Working Principle of an Internal Rotor Motor
Magnetic Field Production
When electrical current flows through the stator windings, it produces a magnetic field around them. This magnetic field interacts with the magnetic field produced by the rotor, causing it to rotate.
Rotational Force Generation
As the rotor rotates, its magnetic field changes orientation relative to the stator's magnetic field. This change in orientation causes a continuous interaction between the two fields, generating a rotational force that keeps the rotor turning.
Torque Production
The rotational force generated by the interaction between the stator and rotor fields produces torque, which drives the mechanical load connected to the motor's shaft.
Speed Control
The speed of an internal rotor motor can be controlled by varying the frequency and amplitude of the electrical current supplied to the stator windings. This allows for precise control over the motor's output speed and torque.
Advantages and Disadvantages of Internal Rotor Motors
Advantages:
- High efficiency due to low friction losses from bearings.
- Compact size and lightweight design make them suitable for various applications.
- Can be designed for high-power output with proper cooling mechanisms.
- Precise speed control through variable frequency drive systems.
Disadvantages:
- More complex construction compared to external rotor motors.
- Requires additional components such as commutators or slip rings for wound rotor designs.
- Maintenance requirements may be higher due to bearing wear and other factors.
- May generate more heat than external rotor motors, requiring effective cooling solutions.
In conclusion, an internal rotor motor works by utilizing the interaction between magnetic fields produced by its stator and rotor components to generate rotational force and torque. While these motors offer many advantages such as high efficiency and precise speed control, they also come with some drawbacks like increased complexity and maintenance requirements.