This text provides a comprehensive overview of the factors affecting the cost of a new product and outlines a step-by-step process for estimating these costs. It emphasizes the importance of accurate cost estimation for ensuring profitability and competitive pricing in the market. The factors discussed include material, labor, manufacturing overheads, R&D, marketing and sales, administrative expenses, capital expenses, transportation and logistics, taxes and duties, and contingency costs. The cost estimation process involves identifying all cost components, estimating individual costs, calculating total cost, determining pricing strategy, and conducting sensitivity analysis. Overall, this text serves as a valuable guide for businesses looking to estimate the cost of a new product accurately and set a competitive price that ensures profitability.
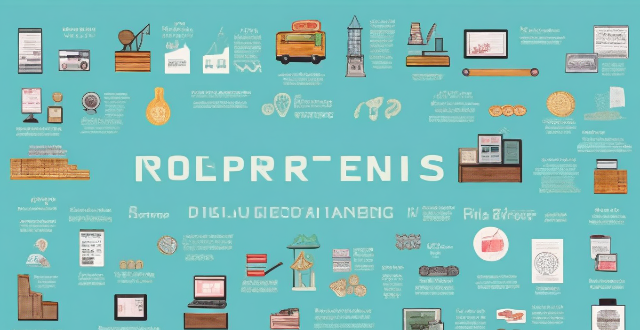
New Product Cost Estimation
Introduction
The cost of a new product is an essential factor that determines its success in the market. It is crucial to estimate the costs accurately to ensure profitability and competitive pricing. In this answer, we will discuss the various factors that contribute to the cost of a new product and provide a detailed estimation.
Factors Affecting Product Cost
1. Material Costs: The cost of raw materials required for producing the product.
2. Labor Costs: The wages paid to employees involved in the production process.
3. Manufacturing Overheads: Expenses related to manufacturing, such as rent, utilities, and maintenance of equipment.
4. Research and Development (R&D) Costs: Expenses incurred during the product development phase, including research, design, and testing.
5. Marketing and Sales Costs: Expenses associated with promoting and selling the product, such as advertising, packaging, and distribution.
6. Administrative Expenses: General overhead costs, such as office rent, salaries, and insurance.
7. Capital Expenses: Costs associated with purchasing or leasing equipment, buildings, or other assets used in production.
8. Transportation and Logistics Costs: Expenses related to transporting raw materials and finished products to and from the manufacturing facility.
9. Taxes and Duties: Government-imposed taxes and duties on raw materials, products, or services.
10. Contingency Costs: Unexpected costs that may arise during the production process, such as machine breakdowns or delays in supply chain.
Cost Estimation Process
To estimate the cost of a new product, follow these steps:
Step 1: Identify all cost components
List down all the factors affecting the product cost mentioned above.
Step 2: Estimate individual costs
For each cost component, estimate the expected cost based on market research, supplier quotes, or internal data.
Step 3: Calculate total cost
Add up all the estimated costs to get the total cost of producing one unit of the product.
Step 4: Determine pricing strategy
Consider the target market, competition, and desired profit margin to determine the final selling price of the product.
Step 5: Conduct sensitivity analysis
Analyze how changes in individual cost components can affect the overall cost and profitability of the product.
Conclusion
Estimating the cost of a new product involves considering various factors and conducting thorough research. By following the cost estimation process outlined above, you can accurately determine the cost of producing your product and set a competitive price that ensures profitability.